How RFID Technology Fixes Stock Inaccuracy at Scale
Posted on juin 3, 2024Inventory mistakes are more expensive than most businesses realize.
Missed sales, overstock, and out-of-stock emergencies — they all come down to inaccurate stock data.
For years, barcodes and spreadsheets have tried to keep inventory under control. But as operations scale, these tools can’t keep up. Manual tracking slows teams down. Human errors slip in. Data gets delayed or lost.
RFID technology changes that.
By using smart tags that don’t need line-of-sight scanning, RFID lets businesses track stock in real time — automatically. That means faster counts, fewer errors, and up to 99% inventory accuracy. It also means cutting labor costs, reducing loss, and gaining visibility across every warehouse or store.
In this guide, you’ll learn how RFID systems actually work, why they outperform traditional tracking methods, and how they help companies build smarter, more scalable operations.
Let’s explore how RFID technology is solving stock inaccuracy — at scale.
Why RFID Technology Is Essential for Modern Inventory Tracking
Modern inventory systems aren’t just about keeping count —they’re about keeping up. As supply chains become more complex, businesses need real-time visibility, faster stock checks, and data accuracy that manual systems simply can’t deliver.
That’s why RFID is becoming the backbone of scalable inventory operations.
Unlike barcodes, which require line-of-sight scanning and manual effort, RFID systems use radio waves to automatically detect and track tagged items — even in bulk and without direct scanning. This alone can speed up inventory processes by over 25%, according to industry benchmarks.
But the real impact goes deeper:
-
Real-Time Visibility: RFID gives businesses the ability to track items across warehouses, retail locations, or transit hubs without manual input.
-
Reduced Human Error: No more missed scans or data entry mistakes. RFID automates identification and logging.
-
Higher Stock Accuracy: Businesses using rfid inventory technology for accuracy rates above 99%, compared to 85–90% with traditional systems.
-
Operational Speed: Inventory counts that once took hours can be completed in minutes.
-
Scalability: RFID scales easily — from small storage rooms to multi-location warehouse networks.
RFID isn’t a luxury anymore. It’s becoming the standard for businesses that want to move faster, waste less, and manage inventory with confidence.
RFID Tags for Inventory: Types, Use Cases & ROI
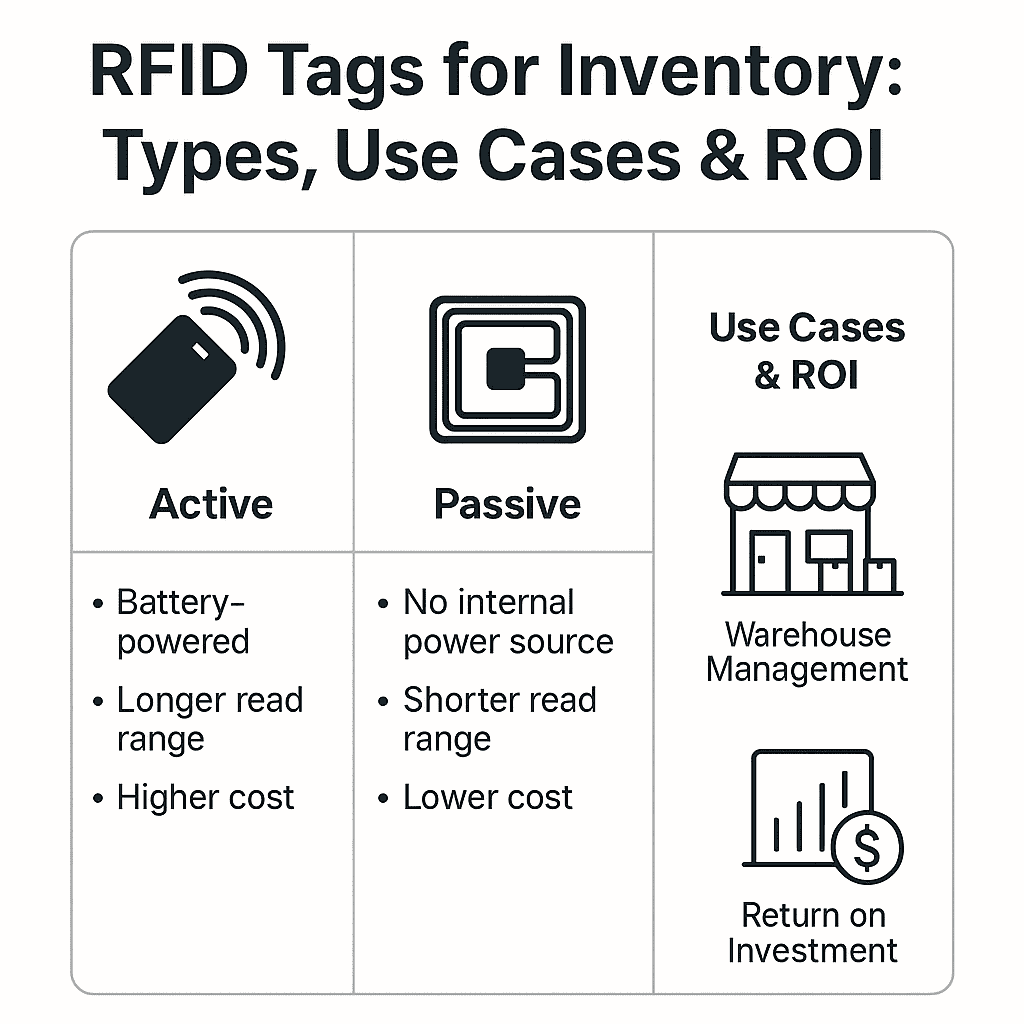
RFID tags are the core of any RFID system — and choosing the right type makes a big difference in how accurately, efficiently, and cost-effectively you can manage inventory.
Unlike barcodes, which must be scanned one-by-one, RFID tags can be read in bulk, without line-of-sight, saving time and eliminating bottlenecks in warehouse workflows.
Types of RFID Tags Used in Inventory
Tag Type | Description | Best Use Case |
---|---|---|
Passive RFID Tags | No battery, activated by reader signal | Inventory of low-cost or fast-moving goods |
Active RFID Tags | Built-in battery, longer read range | High-value assets, large warehouses |
Semi-Passive Tags | Battery-powered but only for sensors | Cold chain, condition-sensitive items |
Each tag type comes with trade-offs in cost, read range, and durability — which is why selecting the right one depends on your inventory type, volume, and environment.
Real-World Use Cases
-
Commerce: Clothing brands use passive RFID tags to track apparel across distribution centers and sales floors, reducing out-of-stock issues by up to 50%.
-
Logistics: Shipping and fulfillment centers use active RFID tags to monitor packages in transit — minimizing misroutes and losses.
-
Healthcare: Hospitals track equipment, medication, and supplies in real time to ensure availability and avoid critical shortages.
-
Production: Factories embed RFID into pallets and bins to monitor raw material flow and reduce production delays.
The ROI of Using RFID Tags in Inventory
Investing in RFID tags in inventory isn’t just a tech upgrade — it’s a cost saver:
-
Inventory Accuracy Boost: From ~85% to 99%+ with RFID
-
Labor Cost Reduction: RFID-enabled inventory counts are up to 30% faster than manual ones
-
Loss Prevention: Automated visibility reduces shrinkage, misplacement, and theft
-
Operational Efficiency: Faster receiving, stocking, and cycle counts
-
Scalability: RFID infrastructure grows as your operations grow, with minimal additional setup
In short, RFID tags let businesses do more with less — less time, less labor, and fewer mistakes — while gaining more control, insight, and profit.
RFID vs Barcode: What’s the Real Difference in 2025?
Barcodes have been the default tracking method for decades — but they’re no longer enough for businesses that need speed, accuracy, and visibility at scale.
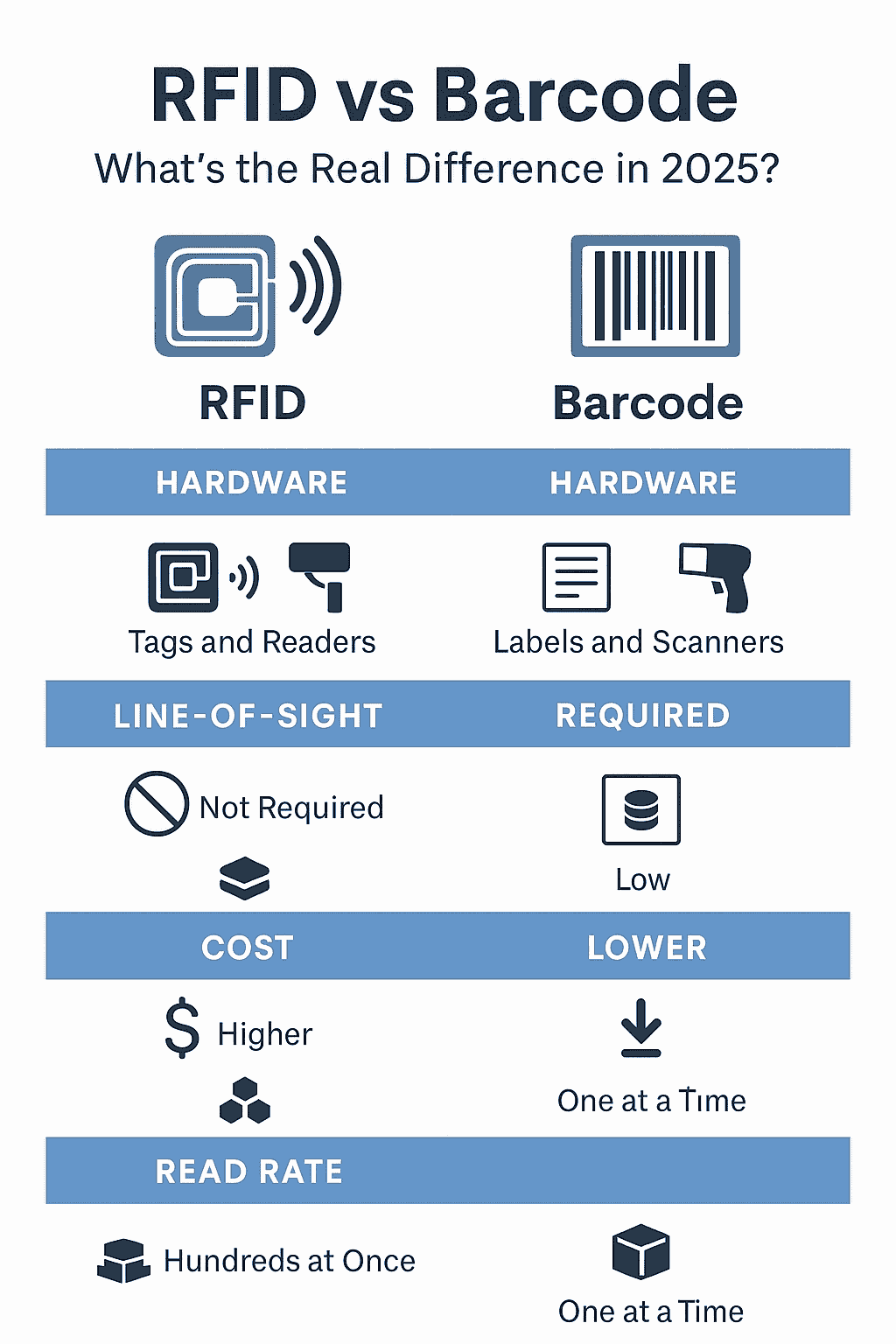
In 2025, RFID technology isn’t just an alternative — it’s a strategic advantage.
Here’s how they really compare:
RFID vs Barcode Comparison Table
Feature | Barcode | RFID |
---|---|---|
Scan Method | Requires line-of-sight | No line-of-sight needed |
Read Speed | One item at a time | Hundreds of items in seconds |
Durability | Prone to wear, scratches, smudges | Weather-resistant, rugged options |
Setup Cost | Low initial cost | Higher upfront investment |
Ongoing Cost | Manual scanning labor | Reduced labor + automation savings |
Data Storage | Basic ID only | Rich data (location, time, condition) |
Accuracy Potential | ~85–90% | Up to 99%+ |
Use Case Fit | Small-scale, low complexity ops | High-volume, real-time environments |
Why Businesses Are Upgrading
-
Barcodes are reactive. You only know something’s missing when you scan and realize it’s gone. RFID is proactive — it tells you what’s happening in real time.
-
Barcodes rely on human effort. RFID removes the dependency on manual labor.
-
RFID improves data quality. Each tag can hold more than just an ID — it can store timestamps, locations, and even sensor data (e.g., temperature).
And most importantly:
Businesses using RFID report fewer stockouts, faster inventory cycles. higher ROI — even after accounting for initial implementation costs.
RFID isn’t just a fancier barcode — it’s an entirely different class of tracking technology.
For any business managing large inventories, fast-moving goods, or multi-location operations, RFID is the clear winner.
Real-Time Inventory Tracking: How RFID Changes the Game
For growing businesses, “inventory visibility” isn’t just a buzzword — it’s the difference between efficient operations and constant firefighting.
Traditional systems like barcodes only update inventory when someone manually scans an item. That means your data is always delayed, and often inaccurate.
Avec RFID, tracking becomes automatic, continuous, and real time.
How Real-Time RFID Tracking Works
Each item is tagged with a unique RFID chip. As it moves through your warehouse, retail space, or logistics center, RFID readers automatically capture its location and status — without needing a manual scan.
Benefits of RFID inventory tracking
-
You know exactly what’s in stock, and where
-
Inventory updates happen in real time
-
No blind spots, no lag, no guesswork
What Real-Time Inventory Enables
-
Faster Replenishment: Know immediately when stock levels hit reorder points
-
Smarter Allocation: Move inventory between stores based on real-time demand
-
Improved Customer Experience: Prevents overselling and out-of-stock situations
-
Streamlined Audits: RFID cycle counts can happen during normal operations
In fact, companies that shift to RFID-based inventory tracking report up to 27% improvement in accuracy et significant gains in fulfillment speed, according to research by the Aberdeen Group.
In a world that moves in real time, your inventory system should too. RFID makes that possible — and scalable.
RFID Cost Savings: How It Cuts Errors and Boosts Accuracy
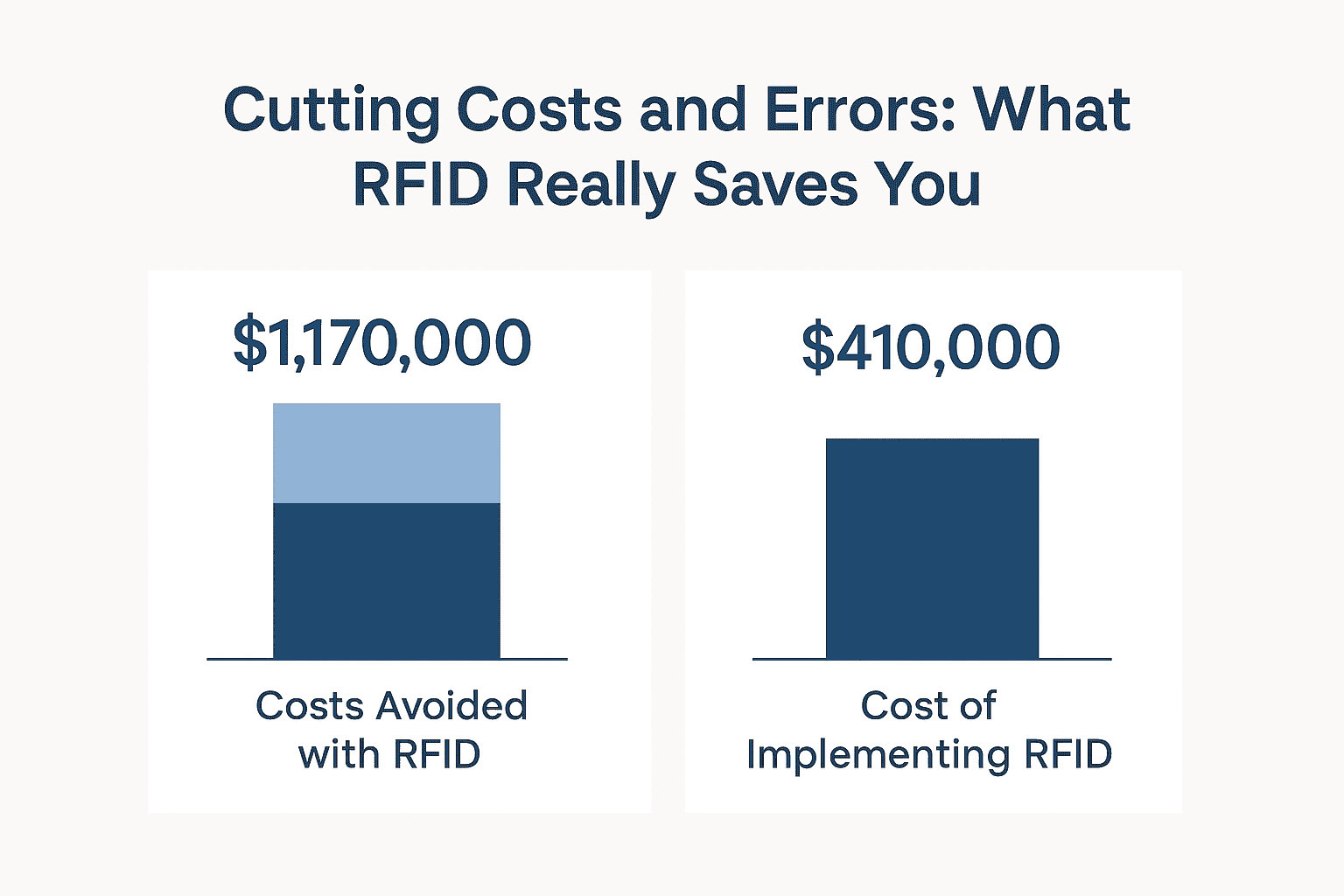
For businesses that still rely on barcodes or spreadsheets, inventory errors and inefficiencies are often seen as “just part of the process.” But they don’t have to be — and they shouldn’t be.
RFID technology isn’t just about better tracking. It’s about measurable savings.
Here’s What RFID Actually Saves You
1. Labor Costs
Manual inventory counting eats up time and staff hours. RFID allows you to:
-
Scan hundreds of items simultaneously
-
Automate cycle counts during normal operations
-
Cut inventory-related labor hours by up to 30%, according to Zebra Technologies
RFID helps reduce human error, but to truly solve the problem, businesses need to understand the operational roots of inventory mismatch. This guide covers what those are — and how to fix them without overhauling everything.
2. Inventory Shrinkage
Whether it’s theft, loss, or misplacement, inventory shrink adds up fast.
RFID systems give you:
-
Real-time accountability for every item
-
Alerts for unexpected movement or missed scans
-
Shrink reduction rates of 20–40% in high-volume environments
3. Stockouts and Overstock
Bad data leads to bad decisions — overordering, emergency replenishments, or missed sales.
With RFID
-
You avoid overstock that ties up capital
-
You prevent stockouts that cost you revenue and reputation
-
Inventory accuracy jumps to 99%+, reducing the need for “safety stock” buffers
- Reduce stockouts and prevent revenue loss
4. Lost Time = Lost Money
-
Faster receiving, faster audits, faster order fulfillment
-
Time saved = cost saved
-
Many RFID users report operational cost reductions of 10–15% overall
Real-World ROI in Numbers
-
A leading retailer reported 98% boost stock accuracy at scale across 500 stores post-RFID rollout
-
A logistics provider reduced package misroutes by 30%
-
A healthcare chain cut medical equipment losses by 40% in the first year of RFID use
The hidden cost of manual inventory systems is bigger than most companies realize. RFID turns that hidden drain into a controllable, measurable gain.
Case Studies: RFID in Retail, Logistics, and Healthcare
RFID isn’t a concept. It’s a proven system that’s helping companies across industries save time, money, and inventory headaches — at scale.
Here’s how it’s playing out in the real world example of RFID in Stock Accuracy in Supermarkets:
Retail: From Chaos to Accuracy Across 500 Stores
A global apparel brand implemented RFID tags across its full inventory chain — from warehouse to store floor.
Results:
-
Inventory accuracy increased from 76% → 98.5%
-
Stockout incidents dropped by 50%
-
In-store cycle counts were completed in 90% less time, freeing up staff for customer service
“RFID gave us the visibility we needed to sell more — not just stock more.”
Logistics: Real-Time Tracking for Thousands of Shipments
A third-party logistics (3PL) provider added RFID to its transit packaging system to track containers moving between fulfillment hubs.
Results:
-
Misrouted packages reduced by 30%
-
Package location data updated every 60 seconds
-
Reduced inbound verification time by 40%
“We stopped losing things — and we stopped losing time.”
Healthcare: Smarter Equipment Tracking, Fewer Errors
A hospital group deployed RFID on critical medical equipment and high-value medication carts.
Results:
-
Equipment retrieval time reduced by 40%
-
Inventory loss of medical devices dropped by over 35%
-
Improved patient care by reducing delays in access to essential tools
“RFID helped us get life-saving equipment to the right place — fast.”
These real-world wins are just a few examples of what RFID can deliver when implemented with clear goals and the right infrastructure.
Whether you’re managing products, packages, or patients — RFID brings the clarity, speed, and control that legacy systems just can’t match.
How to Choose the Right RFID Inventory System
By now, it’s clear that RFID isn’t just more efficient — it’s transformational. But the benefits you get depend entirely on how well you choose and implement your system.
Here’s how to get started the right way:
1. Clarify Your Inventory Challenges
Before choosing tech, define the problem. Ask:
-
Are we dealing with stockouts? Shrinkage? Slow counts?
-
Do we lack real-time visibility across locations?
-
Is labor-intensive tracking slowing us down?
A great RFID system is one that directly solves your most expensive inventory pain points.
2. Choose the Right Type of RFID Tags
Tag selection is crucial. Consider:
-
Passive tags for low-cost, high-volume goods
-
Active tags for high-value or long-range tracking
-
Environmental factors (heat, cold, metal interference)
3. Match Readers to Your Operational Flow
-
Fixed readers for chokepoints (dock doors, entry/exit zones)
-
Handheld readers for flexible cycle counts
-
Mobile apps for real-time visibility on the go
The best setups don’t slow down your team — they disappear into your workflow.
4. Integrate With Your ERP or WMS
Without data sync, RFID is just fancy tracking.
Make sure your system integrates with:
-
Your ERP (for purchasing, stock levels, financials)
-
Your WMS (for bin-level accuracy, pick/pack flow)
-
Your analytics dashboard (for performance insights)
5. Calculate ROI Before You Deploy
Look beyond just “tag + reader” costs. Consider:
-
Labor hours saved
-
Shrinkage prevented
-
Stock accuracy gained
-
Capital unlocked from excess inventory
Not sure where to start? Try using an ROI calculator to estimate how fast your investment can pay off — sometimes in under 6 months.
Pro Tip:
Start with a pilot implementation in one warehouse or product category.
Validate the impact, then scale confidently.
Why RFID Tech Is the Future of Inventory Management
If inventory accuracy, speed, and visibility matter to your business — then RFID isn’t optional anymore. It’s essential.
Across industries, RFID technology has moved from “nice-to-have” to mission-critical infrastructure. It solves the real-world problems that barcode systems and spreadsheets can’t:
-
Stock inaccuracy that kills revenue
-
Labor-intensive audits that drain resources
-
Lack of real-time data that causes bad decisions
From retail to logistics to healthcare, businesses are unlocking up to 99% accuracy, faster fulfillment, fewer losses, and real-time control — all thanks to RFID.