Why RFID Warehouse Tracking Fails — And How to Make It Actually Work
Posted on May 28, 2024Still struggling with missing items or slow counts — even after switching to RFID?
Most warehouse leaders expect RFID to solve everything, but without the right system, it just adds complexity.
The truth? RFID can drastically improve speed and stock accuracy — but only when implemented the right way.
In this guide, we’ll break down how RFID works in real warehouse workflows, common mistakes, and the strategies that actually deliver ROI.

What Is RFID Warehouse Tracking, Really?
RFID (Radio Frequency Identification) warehouse tracking is a system that uses smart tags and wireless signals to automate the identification and tracking of inventory.
Each item is tagged with an RFID chip — think of it like a barcode that doesn’t need to be seen to be scanned. Instead of manually scanning boxes one-by-one with a gun, RFID readers automatically detect dozens (or hundreds) of items at once, even through boxes, shelves, or pallets.
This means no line of sight is needed. Stock counts that used to take hours can now be done in minutes — with accuracy that hits 99% or more.
RFID tracking is especially powerful in high-volume warehouses or complex environments where
-
You need real-time visibility of item locations
-
Traditional barcode systems fall short
-
Manual errors and stock inaccuracies hurt profitability
Top 5 Reasons RFID Tracking Fails in Warehouses
For all the hype around RFID, many warehouses still struggle to make it work.
And here’s the kicker — it’s not the technology’s fault.
Most failures happen because companies treat RFID like a plug-and-play solution. It’s not.
Here are the most common reasons RFID flops in real operations:
1. Wrong Tag Selection
Not all RFID tags are created equal. Using the wrong type (LF, HF, UHF) for the environment or material (e.g., metal, liquids) leads to inconsistent reads. Before choosing between UHF, NFC, or active tags, make sure you understand which RFID tag you should use for your specific business model and tracking needs.
2. Poor Reader Placement
Readers can’t read what they can’t “see.” Bad placement creates blind spots, missed items, and scanning chaos.
3. No Integration With WMS or ERP
Without a seamless data flow into your warehouse management system or ERP, RFID becomes just another disconnected tool.
4. Incomplete Staff Training
RFID works best when everyone on the floor knows how it fits into the process. Lack of training = wasted tech.
5. Unrealistic Expectations
RFID doesn’t fix broken workflows — it amplifies them. If your warehouse processes are flawed, RFID will only make the mess louder.
How to Make RFID Warehouse Tracking Actually Work — Step-by-Step
Many RFID projects fail not because of the tech, but because of poor planning and integration. Here’s a proven 7-step framework to deploy RFID that actually improves inventory accuracy, reduces costs, and scales with you.
1. Conduct a Site Audit & Signal Test
Before you even choose hardware, assess your warehouse layout. Use RFID signal mapping tools to identify choke points, metal interference, and blind zones. You can’t fix what you don’t measure.
2. Choose the Right Tags for Your Inventory
Not all RFID tags are created equal. High-moisture? Metal surfaces? Frozen goods? You need UHF or specialized tags — not the cheapest option from Alibaba. Match tag specs to use cases.
3. Optimize Reader Placement
Reader misplacement is the #1 reason RFID fails. Set up field tests to validate scan range and eliminate dead spots. Use ceiling-mount antennas, gate systems, or handhelds depending on flow.
4. Integrate RFID with Your WMS
This is where most projects die. Don’t just dump RFID data into Excel — sync it directly with your WMS via API or middleware. Data must update real time, not in batches.
5. Run a Pilot—Then Scale
Test on a single zone or SKU category. Track KPIs like scan accuracy, shrinkage rate, and count speed. If it works? Scale up. If it doesn’t? Diagnose and fix before rollout.
6. Train Your Staff & Build SOPs
Even the best tech fails without buy-in. Train warehouse staff on how RFID fits their daily flow. Write SOPs. Set accountability.
7. Monitor KPIs & Continuously Improve
Track accuracy percentage, cycle count time, shrinkage, and time-to-locate metrics. RFID should reduce cost per count and improve fulfillment speed. If not, you’ve got gaps.
For example: A mid-size apparel retailer implemented RFID in their 3 distribution centers. Their initial pilot had only 68% scan accuracy — due to poor reader placement and generic tags. After a warehouse audit and switching to anti-metal UHF tags, their scan rate jumped to 98.4% and cycle count times dropped by 42% within one quarter.
The Real Benefits of RFID When Implemented Right
When RFID is properly planned and integrated, the results are game-changing — especially in fast-moving, high-volume warehouse environments.
Here’s what “working RFID” actually looks like:
Inventory Accuracy Jumps to 99.9%+
Say goodbye to blind spots. RFID scans hundreds of tags simultaneously, ensuring your system matches physical stock — in real time.
Shrinkage Drops Like a Rock
With RFID, every item’s movement is logged automatically. Theft, misplacement, or manual entry errors? Instantly traceable.
Faster Audits, Happier Teams
Full warehouse counts that took days? Done in hours. RFID slashes labor hours and cuts operational costs.
Real-Time Visibility Across Locations
Need to see what’s in Store #42 or Warehouse B right now? RFID-connected dashboards show it live — not three days later from a spreadsheet.
Automation That Works With You
RFID doesn’t just track items — it triggers alerts, auto-reorders, and syncs with your WMS/ERP to keep operations smooth.
How RFID Integrates with Your Existing Systems
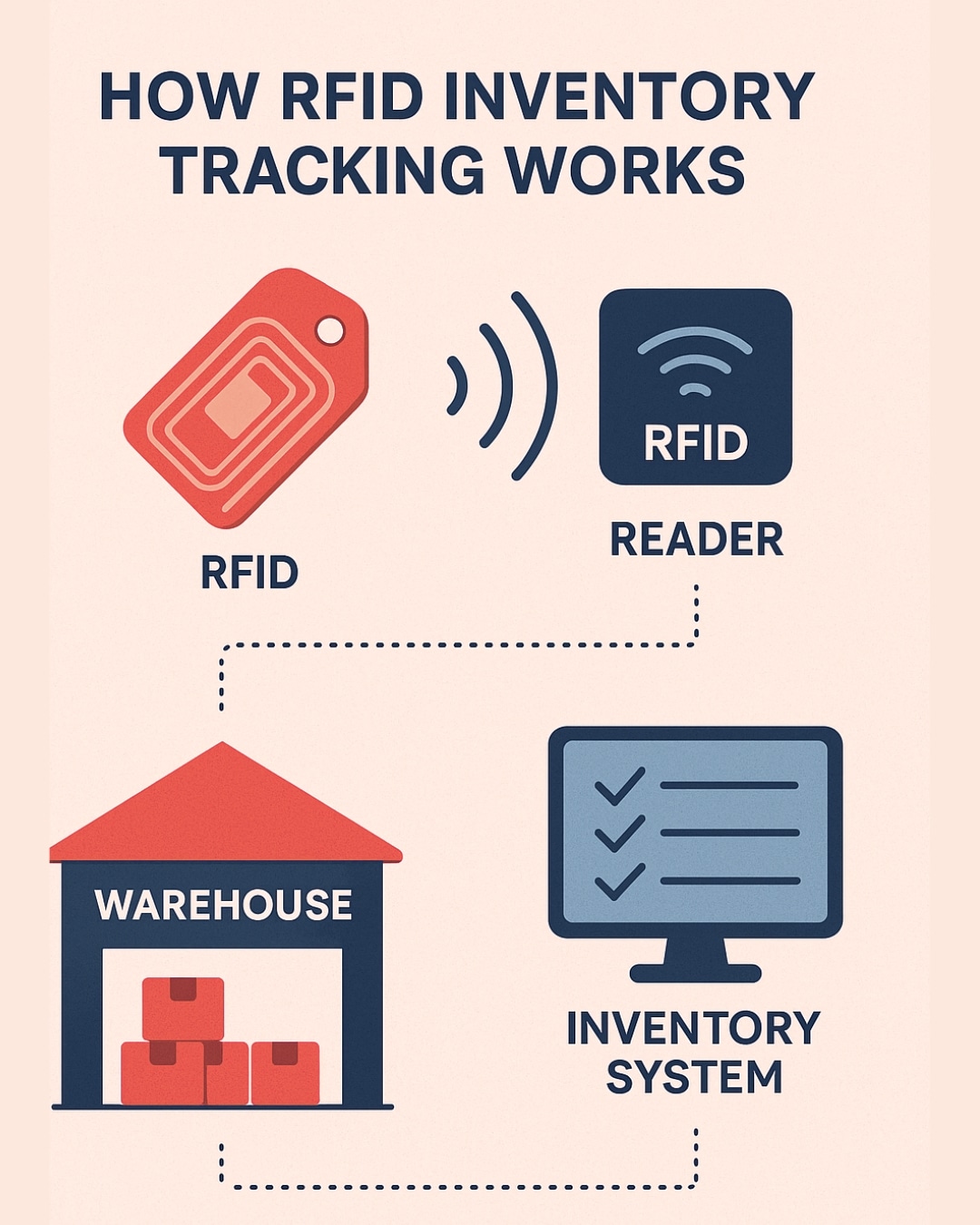
One of the biggest misconceptions about RFID is that it requires a full tech overhaul. It doesn’t.
When done right, RFID complements your existing tools — from warehouse management systems (WMS) to enterprise resource planning (ERP) platforms.
Warehouse Management System (WMS) Integration
RFID feeds real-time inventory data directly into your WMS. This allows for:
-
Live updates on stock levels
-
Automated location tracking
-
Faster order picking and replenishment
ERP System Sync (SAP, NetSuite, Oracle)
Integration with ERP platforms means inventory data doesn’t live in isolation. It connects purchasing, logistics, sales, and finance for smarter decision-making.
-
Reduced data silos
-
Better demand forecasting
-
Improved inventory valuation
Cycle Count Automation
RFID-enabled cycle counting means you can scan items during normal operations — no shutdowns, no night shifts.
This drastically improves count frequency and accuracy while saving time and labor costs.
If you’re using a legacy system or planning to upgrade, RFID can still be layered in. The key is to work with specialists who understand integration and can customize the setup to match your tech stack.
Interested in what this looks like in practice?
Visit our RFID-powered cycle counting platform Al Tracker for a live example.
RFID vs Barcode: Which One Is Right for You?
Many warehouse teams assume RFID is automatically better than barcodes. But that’s not always true.
The right tracking method depends on your inventory complexity, speed requirements, and budget.
Here’s how they compare:
Feature Barcode RFID Scan Method Line-of-sight (manual) No line-of-sight (automated) Read Speed One at a time Hundreds at once Durability Vulnerable to wear/tear More durable, weather-resistant Setup Cost Low Higher upfront Ongoing Cost Minimal Moderate (tags, readers, integration) Data Storage Basic (ID only) Rich data (location, status, timestamp) Use Case Fit Low volume, low complexity High volume, complex ops
When RFID Is the Smarter Play:
-
Multiple locations or thousands of SKUs
-
Frequent miscounts or shrinkage issues
-
Need for speed and automation
RFID in Warehousing — Industry Stats Snapshot
Metric | Insight |
---|---|
99.9%+ Accuracy | Warehouses using RFID see inventory accuracy jump from 63% (barcode) to 99.9%. (Source: GS1 US) |
25% Faster Order Fulfillment | RFID-enabled warehouses reduce order picking time by up to 25%. (Source: Zebra Technologies) |
30–40% Labor Savings | Automated counts via RFID cut labor time by 30–40%. (Deloitte) |
20% Shrinkage Reduction | Real-time tracking slashes shrinkage rates significantly. (AIM Global) |
ROI in Under 18 Months | Most RFID investments break even within 12–18 months. (RFID Journal) |
RFID Tracking in Warehousing — SWOT Breakdown
Strengths | Weaknesses |
---|---|
✅ Real-time tracking with 99%+ accuracy | ❌ Higher upfront cost vs. barcodes |
✅ No line-of-sight needed — read multiple tags at once | ❌ Tag interference from metal/liquids |
✅ Shrinkage & audit time drastically reduced | ❌ Integration with WMS/ERP requires planning |
✅ Boosts operational visibility & automation | ❌ Requires staff training & SOP redesign |
Opportunities | Threats |
---|---|
Global scalability across regions and store networks | Implementation failure from poor planning (reader/tag misplacement) |
Strong synergy with AI & IoT for smart warehousing | Weak pilot execution can stall or block full adoption |
Significant long-term cost reduction in labor and shrinkage | Risk of vendor lock-in or incompatible hardware decisions |
Improved compliance tracking (e.g., FIFO, expiry management) | Information overload if data isn’t filtered or structured well |
Still unsure which fits your business?
Learn how miscounts and data gaps happen in barcode-only setups in our article on inventory record inaccuracies
What’s Next: AI, Smart Warehouses, and RFID 2.0
RFID isn’t the end of the road — it’s the foundation for the next generation of intelligent warehouses. As technology evolves, RFID is becoming more powerful when combined with tools like AI and real-time data systems.
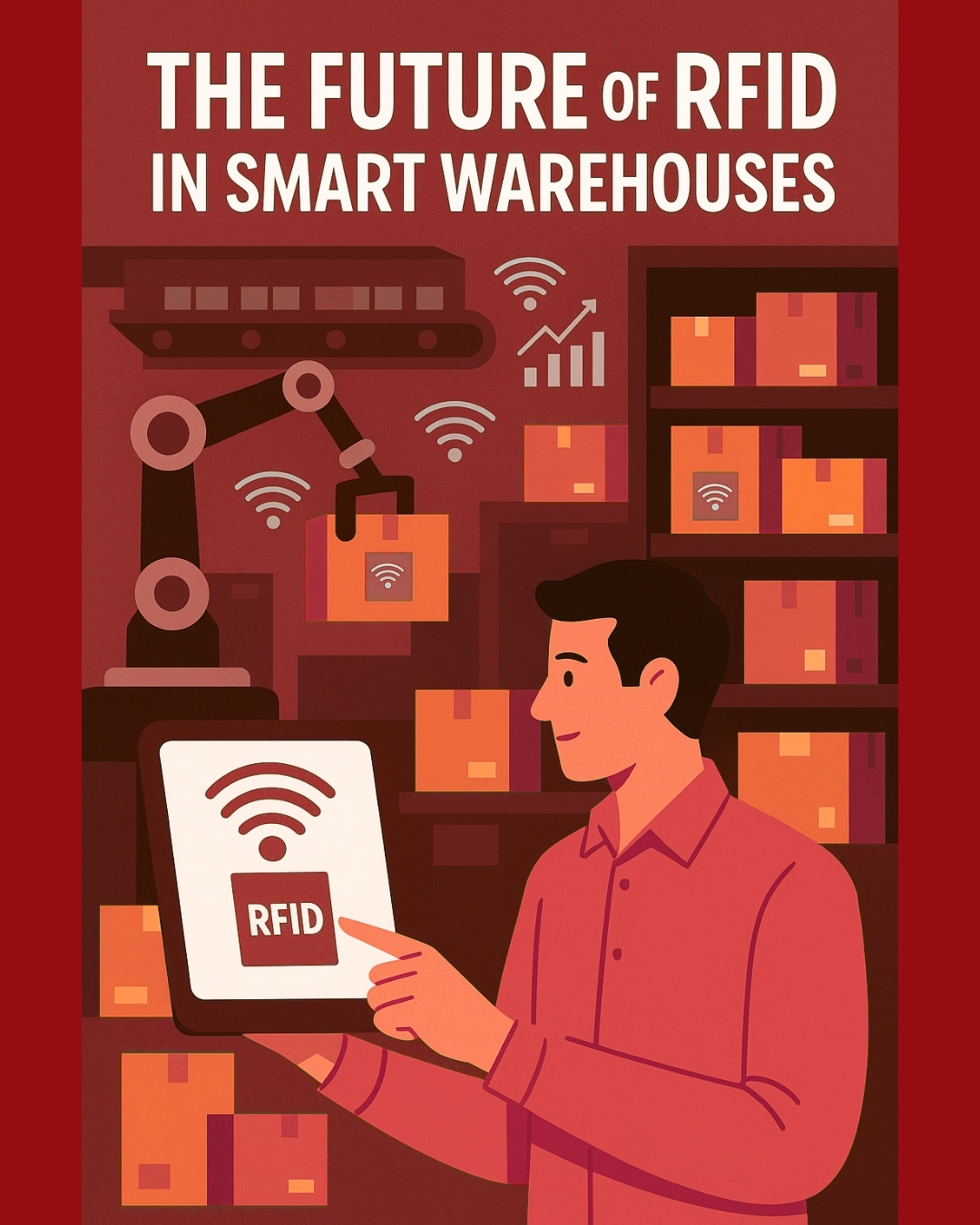
AI-Powered Inventory Forecasting
Imagine RFID not just tracking where things are, but predicting when you’ll run out. AI tools can process RFID data to forecast demand, optimize reorders, and minimize overstock.
Smart Dashboards for Instant Decision-Making
RFID-connected dashboards are no longer passive. With real-time analytics, you get alerts, trends, and suggestions — not just numbers.
Integration With IoT and Blockchain
The most advanced supply chains now use RFID data to feed blockchain networks (for traceability) and IoT devices (for condition tracking like temperature or humidity).
Scalability Without Complexity
RFID 2.0 systems can scale across 100+ stores, multiple countries, or a mix of retail and warehousing without losing visibility.
If your warehouse strategy still relies on spreadsheets and barcode audits, this is your signal to upgrade.
How to Actually Make RFID Work: A Step-by-Step Plan
If you’re planning to implement RFID (or already tried and failed), this five-step framework will help you approach it the right way — strategically and sustainably.
1. Assess Your Inventory Complexity and Environment
Start by identifying:
Number of SKUs
Types of items (metal, liquid, high-shrinkage?)
Warehouse layout and workflows
This helps you decide the right type of tags, readers, and placement.2. Choose the Right RFID Tags and Hardware
Whether it’s UHF for pallets or HF for retail, matching tag type to use case is critical.
Also ensure readers are durable, fast, and work in your specific environmental conditions.3. Integrate With Your WMS and ERP
RFID can’t live in a silo.
Make sure data syncs in real time
Build dashboards for visibility
Use automation rules for replenishment, reordering, and alerts
4. Pilot in a Controlled Zone
Start with one warehouse zone or store.
Measure read accuracy, speed, and stock variance.
Optimize the placement of readers, staff workflows, and tagging protocols.5. Scale Up Strategically
Once the pilot works, scale across locations.
Create SOPs, train teams, and optimize based on real-world feedback.
Expect ongoing refinement — this is not a set-it-and-forget-it tool.
Ready to build a custom RFID implementation plan for your warehouse?
Talk to Altavant’s RFID team to get a tailored strategy and see where you’re losing time and money today.
Final Thoughts—From Struggle to Scalable RFID Success
RFID warehouse tracking isn’t a silver bullet — but it can be a game-changer when implemented the right way.
Whether you’re stuck with poor read rates, failed pilots, or slow manual audits, the solution isn’t more tech — it’s better strategy.
With the right RFID setup, you get:
Inventory accuracy over 99%
Real-time visibility across all locations
Faster cycle counts, lower shrinkage, and smarter decisions
But getting there takes a plan — and often, a partner.
Altavant Consulting helps businesses unlock RFID’s full potential without the trial-and-error. From tag selection to ERP sync, we handle the complexity so your team can focus on scaling operations.
Need to Fix a Broken RFID Rollout?
Altavant Consulting specializes in helping businesses implement RFID the right way — with real-time audits, WMS integration expertise, and a data-first approach. If your system is underperforming, we’ll help you turn it around fast.
📅 Schedule a free 30-minute strategy call now — let’s make your RFID investment actually pay off.