6 Hidden Causes of Inventory Inaccuracy — And How to Fix Them
Posted on December 7, 2023Your Inventory Is Lying — Here’s the Real Cost
Data is crucial in the retail and supply chain management industries. But what happens when the very data you rely on—your inventory records—is quietly betraying your business?
Most teams don’t realize there’s a problem until it’s too late: stockouts, overages, missed sales, and chaotic audits. These are just symptoms of a deeper issue—inventory inaccuracies that grow silently over time, often hidden by outdated processes, human error, and system blind spots.
Inaccurate inventory records aren’t just an operational nuisance. They bleed profit, disrupt customer experience, and weaken decision-making across the business. A 2024 industry report revealed that companies lose billions annually due to inventory discrepancies—not from major system failures, but from routine errors that go uncorrected for months.
This article breaks down the 6 most common, hidden causes of inventory inaccuracy and how you can begin fixing them today—before they impact your bottom line further. Many retailers underestimate the impact of inaccurate inventory data on business performance, leading to decisions based on faulty assumptions.
What Causes Inaccurate Inventory Records?
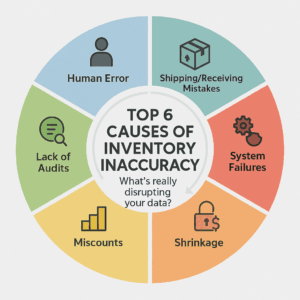
Inventory records become inaccurate when the physical stock in your warehouse or retail location no longer matches what’s reflected in your inventory management system. This mismatch can happen gradually or suddenly—but in either case, the root causes are often predictable, preventable, and, unfortunately, ignored.
The following are the most frequent causes of inaccurate inventory data:
-
Human Error—Manual data entry, skipped scans, or incorrect returns handling can cause inventory records to drift away from reality, especially when accuracy isn’t enforced at the operational level.
-
System Failures—When systems don’t talk to each other—or worse, crash altogether—errors propagate silently. Poor integration between POS, ERP, and warehouse systems leads to double entries, mismatched stock counts, and missing transaction logs.
-
Shipping and Receiving Issues— Mislabeled shipments, lost transfers, and incorrect receiving processes create discrepancies that are rarely corrected in time.
-
Shrinkage and Theft—Unrecorded loss due to internal or external theft, as well as spoilage or damage, is one of the most underestimated causes of inventory distortion.
-
RFID and Automation Gaps – Technology promises efficiency, but when RFID tags are missing, poorly placed, or misconfigured, they can report false positives—suggesting items are in stock when they are not.
-
Lack of Regular Audits—The longer you go without physical cycle counts or reconciliation, the more likely it is that your system will drift from reality. Over time, minor discrepancies snowball into major blind spots.
These causes often operate in combination. A small data entry mistake today, paired with an outdated process and no audit for three months, results in serious variance by the time it’s noticed—if it’s ever noticed at all.
Human Error — The #1 Cause of Inventory Discrepancy
No matter how sophisticated your systems are, human error remains the most common and persistent cause of inventory discrepancies.
Error Type | Real-World Example | Result |
---|---|---|
Double Scanning | Item scanned twice at POS | Overstated inventory levels |
Missed Scans | SKU skipped during receiving | Underreported on-hand stock |
Wrong Quantity Entry | Entered “100” instead of “10” | Phantom inventory in system |
Return Not Logged | Returned item skipped from stock-in | Inventory marked as sold |
Manual Override | Adjustment not properly documented | Breaks audit traceability |
At almost every stage of the inventory lifecycle—from receiving, stocking, and selling to returns and transfers—manual actions create room for mistakes. These errors, while often minor in isolation, compound over time and undermine the integrity of your entire inventory database.
Common Human Errors That Skew Inventory Accuracy:
-
Double Scanning or Missed Scans
Employees might scan the same item twice or miss a scan entirely during checkout or restocking. The result? Your system shows more or less inventory than what’s actually on the shelf. -
Incorrect Returns Handling
When returns are processed without proper documentation or scanning, they either never re-enter inventory or get misclassified. Over time, this leads to overstatements or gaps in stock levels. -
Manual Data Entry Mistakes
Whether during receiving or adjustment, entering “100 units” instead of “10” can create false stock confidence, affecting ordering and fulfillment decisions. -
Poor Training or SOP Misalignment
Staff unfamiliar with inventory procedures may not follow standard processes—leading to missed steps, skipped entries, or incorrect tagging.
The Impact:
-
Inflated or deflated stock levels in the system
-
Delayed reorders or unnecessary restocking
-
Customer dissatisfaction due to incorrect product availability
-
Compromised audit trails
How to Mitigate Human Error:
-
Use barcode scanning and mobile apps to reduce manual input
-
Standardize returns handling with clear protocols
-
Implement staff training and SOP alignment sessions quarterly
-
Use exception reporting to flag sudden variances in stock levels
Human error isn’t entirely preventable—but its impact can be controlled with the right checks, training, and tools in place. Recognizing it as a key vulnerability is the first step to eliminating avoidable losses in your inventory system.
How Shipping & Receiving Mistakes Create Stock Discrepancies
Even with accurate systems and trained staff, inventory records can quickly fall apart if your shipping and receiving processes aren’t airtight.
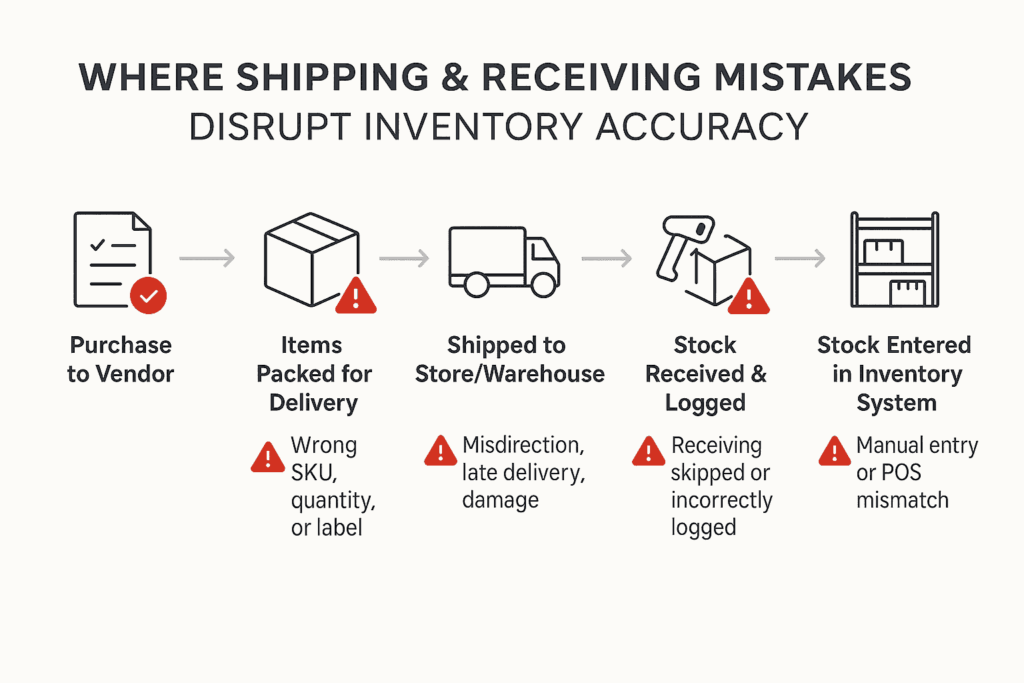
Every time goods move—whether between warehouses, stores, or vendor shipments—there’s a risk that what was expected doesn’t match what actually arrives. When these mismatches aren’t caught and corrected at the dock or stockroom, they get baked into your inventory system, distorting your data from day one.
Common Breakdown Points:
-
Mislabeled Shipments
Boxes sent to the wrong store or warehouse location create immediate imbalance. One location ends up understocked, while another holds inventory it may not need.Many inventory issues begin right at the receiving dock. Poor documentation and lack of verification contribute heavily to receiving-related discrepancies. -
Unverified Receiving
If shipments aren’t verified against purchase orders or ASN (Advanced Shipping Notices), discrepancies go unnoticed. Items may be accepted without quantity checks or barcode validation. -
Manual Reconciliation Gaps
Teams that manually update received goods often delay updates or forget adjustments entirely, resulting in inaccurate on-hand counts.Even well-trained staff can fall victim to common stocktaking mistakes, such as double scans, skipped SKUs, or poor audit trail recording. -
Partial Deliveries or Substitutions
Vendors occasionally substitute products or deliver partial orders. Without real-time reconciliation, systems reflect expected quantities rather than actual delivered stock.
The Risk:
-
Incorrect stock levels per location
-
Missed replenishment cycles
-
Unplanned stockouts or overages
-
Compromised customer promise dates
-
Vendor billing disputes
Fixes That Close the Loop:
-
Match every shipment to a purchase order or ASN before acceptance
-
Use barcode scanning at dock or receiving areas to validate quantity and SKUs
-
Automate stock intake via mobile or handheld devices
-
Build reconciliation steps into your SOPs with manager-level verification
Shipping and receiving is where inventory accuracy either starts strong—or falls apart immediately. Without precise checks at this entry point, every downstream inventory report will be off the mark.
RFID, Glitches & System Failures — The Tech That Betrays You
Technology has transformed inventory management—but it’s not infallible. Tools like RFID, barcode systems, and inventory software promise speed and accuracy, but when these systems fail—or aren’t properly configured—they quietly undermine your records.
System Failure Type | Example Scenario | Impact on Inventory Accuracy |
---|---|---|
Outdated WMS Software | Warehouse system doesn’t sync real-time stock updates | Stock appears available when it’s not |
POS System Glitch | Transactions fail to subtract items from inventory | Overstated stock levels |
System Integration Gaps | WMS doesn’t update ERP or eCommerce system | Different platforms show conflicting stock data |
Barcode Scanner Failure | Scanner skips items during receiving | Underreported or missing inventory |
Cloud Downtime or Sync Delay | Inventory updates don’t reflect for hours | Inventory sold twice or oversold |
Many retailers assume automation means accuracy by default. But without validation, oversight, and system integration, these digital tools can introduce a false sense of precision.While no system is flawless, modern RFID tracking solutions help bridge the gap between real-time data and shelf accuracy.
Common Technology-Driven Causes of Inaccuracy:
-
Missing or Misplaced RFID Tags
During counts, items without tags or with tags positioned wrongly do not register, resulting in phantom inventory or underreporting. -
Software Glitches
Bugs, crashes, or sync delays between your inventory system and sales platform (POS, ERP, etc.) can result in missing transactions, delayed updates, or duplicated entries. -
Integration Gaps
When systems like point-of-sale, warehouse management, and procurement software don’t communicate in real time, inventory data becomes fragmented. A product sold may still show as in stock in your ERP. -
Unverified System Updates
New feature rollouts or software updates that aren’t tested against real operational workflows can alter how inventory is logged, causing blind errors for weeks.
The Cost of Overreliance:
-
Phantom inventory (items showing available but missing)
-
Lost visibility across channels (especially in omnichannel environments)
-
Delayed order fulfillment due to out-of-sync data
-
Poor audit performance due to inconsistent logs
How to Prevent System-Driven Inaccuracy:
-
Validate RFID/tagging practices regularly and conduct tag audits
-
Ensure full system integration—especially between POS, WMS, and ERP
-
Test all software updates in sandbox environments before rollout
-
Run reconciliation checks to compare system logs with physical stock
Technology only works when your process is tighter than your software. Without disciplined system oversight, automation becomes a liability—not a solution.
Shrinkage, Theft & Lost Stock — The Invisible Killers
Not all inventory discrepancies are caused by process failures or technical glitches. Sometimes, the products are simply gone—and no one noticed.
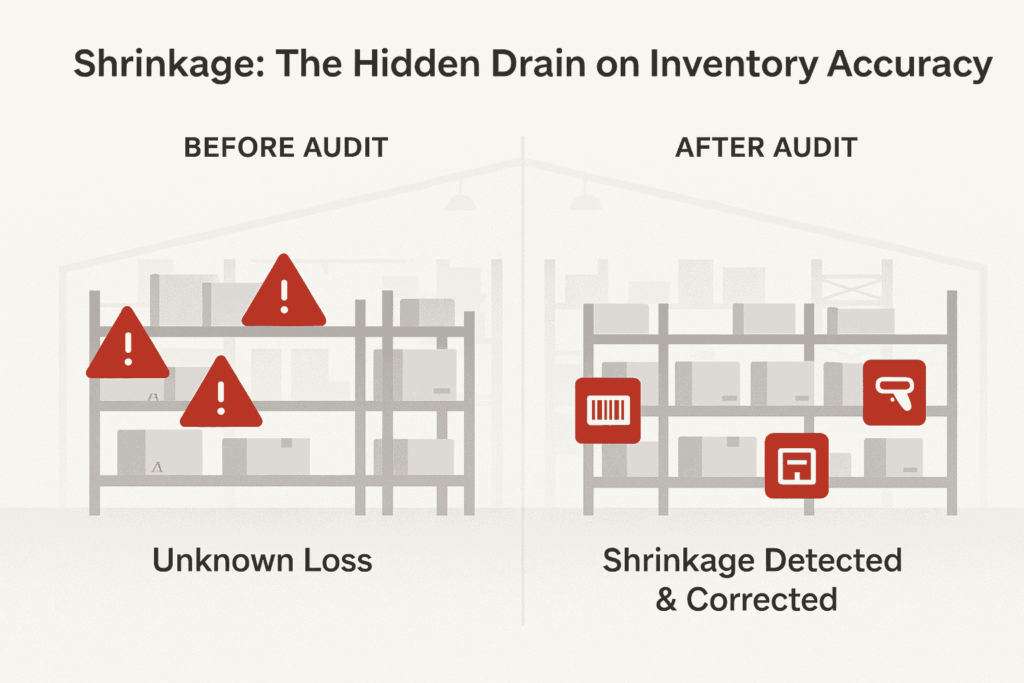
The unrecorded loss of inventory as a result of theft, damage, spoiling, misplacing, or administrative error is referred to as shrinkage. It is one of the most enduring and underappreciated causes of erroneous inventory records, especially in retail settings with high volume.
Where Shrinkage Happens (But Rarely Gets Caught):
-
Internal Theft
Employees bypassing systems to take merchandise or manipulating returns, transfers, or stock adjustments. This is often disguised as “routine loss” unless tightly audited.Understanding the pros and cons of cycle count vs physical count can help you build a sustainable accuracy strategy that doesn’t require warehouse shutdowns. -
External Theft
Shoplifting, organized retail crime, or loss during transportation. These are especially difficult to track without robust security and reconciliation protocols. -
Inventory Misplacement
Items stored in the wrong location or shelved without proper documentation can remain unaccounted for until a full physical audit—if ever. -
Damage or Spoilage
Broken, expired, or unusable inventory that is discarded without being logged still exists in your system as salable stock.
The Real Impact:
-
False stock confidence leading to customer dissatisfaction
-
Triggering replenishment orders for inventory that was never sold
-
Inflated financial reporting
-
Misalignment between reported and physical inventory
How to Reduce Shrinkage:
-
Conduct regular cycle counts, especially for high-risk SKUs or categories
-
Implement surveillance or digital tracking in backrooms and warehouses
-
Establish strict return and transfer protocols
-
Use discrepancy logs and flag patterns over time for investigation
Shrinkage is rarely visible until it’s already hurting your margins. Proactive monitoring, strict control points, and consistent auditing are your best defenses against these invisible killers.One major consequence of inaccurate records is stockouts—leading to missed sales and poor customer experiences. Here’s how to prevent inventory stockouts by addressing data discrepancies early.
The Real Cost of Inventory Inaccuracy (And Why You Can’t Ignore It)
Inventory inaccuracy isn’t just a backroom issue. Over time, it impacts every core function of your business—from sales and customer experience to finance, forecasting, and supply chain stability.
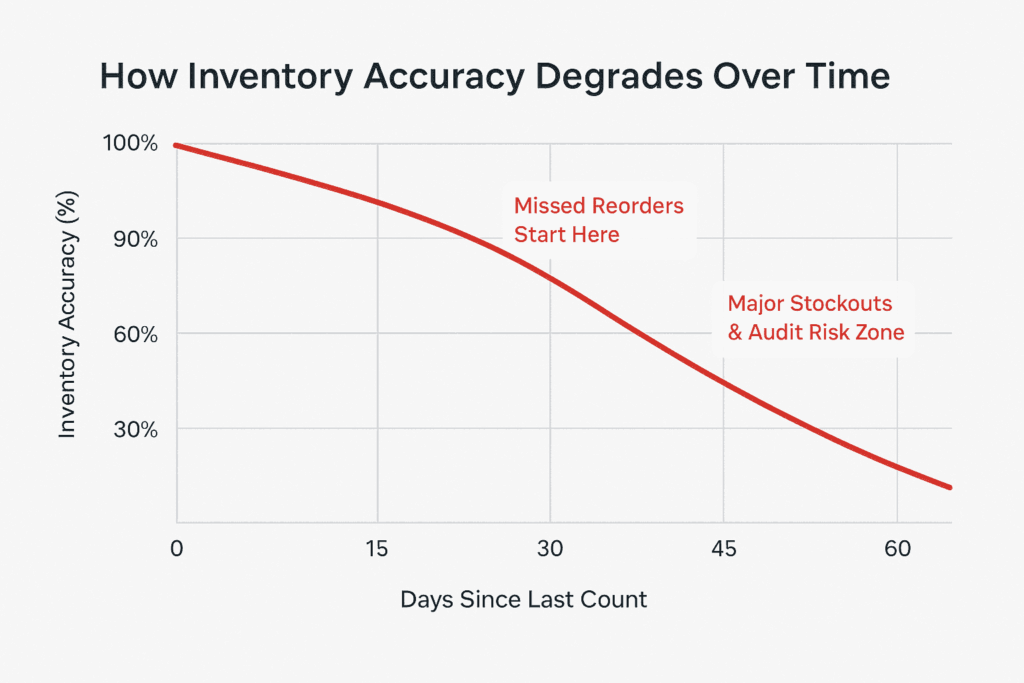
And while a single miscount might seem insignificant, inventory data that drifts over weeks or months quietly builds up to real financial damage.
Tangible Business Costs of Inaccurate Inventory:
-
Lost Sales & Stockouts
When your system says an item is in stock, but it’s not, customers walk away—and they don’t always come back. In high-turnover industries, these losses scale quickly. -
Overstocking & Working Capital Drain
Inventory that isn’t moving—or doesn’t exist but gets reordered anyway—locks up cash. That’s money you can’t spend on growth, marketing, or replenishment of actual bestsellers. -
Customer Experience Failures
Inaccurate availability, delayed shipping, canceled orders—these all erode trust. The risk for omnichannel retailers increases with each platform. -
Financial Misreporting
If inventory is overstated or understated in financial systems, it skews COGS, inflates assets, and creates compliance issues—especially under IFRS or GAAP standards. -
Operational Inefficiency
Time spent chasing stock that doesn’t exist, rechecking discrepancies, or resolving mispicks is time not spent optimizing fulfillment or planning better replenishment cycles.
Industry Snapshot:
A 2023 audit by retail analytics firm IHL found that inventory distortion (including shrinkage and miscounts) accounts for over $1.8 trillion in global annual losses, combining stockouts and overstocks. Most of this is preventable.
What This Means for You:
If inventory inaccuracy is still being treated as a low-priority operational issue, it’s already costing your business in ways that aren’t fully visible yet. Fixing it isn’t about avoiding embarrassment during an audit—it’s about protecting revenue, retaining customers, and restoring confidence in your data.
How to Fix Inventory Inaccuracy (Without Going Crazy)
Fixing inventory inaccuracy doesn’t require a complete system overhaul—but it does require a focused, process-driven approach. Most organizations try to fix symptoms (like missed shipments or stockouts) instead of addressing the root causes that compromise inventory accuracy in the first place.By implementing efficient cycle counting, discrepancies are resolved faster, keeping your system in sync with physical stock.
Here’s how to regain control—without disrupting your operations.
1. Implement Frequent Cycle Counts
Instead of waiting for quarterly or annual full counts, adopt continuous cycle counting across your inventory. Prioritize high-velocity, high-risk, and high-value items. This allows you to catch discrepancies early and reduce large-scale miscounts.
-
Use a rotating schedule to cover your entire catalog monthly or quarterly
-
Automate count scheduling based on SKU velocity or margin
-
Track variances between system and physical counts over time
2. Standardize Receiving and Returns Protocols
Receiving is one of the most common points where inventory records go wrong. Ensure every shipment is verified against a PO and physically scanned in. The same applies to returns—treat every item as a transaction that affects live inventory.
-
Match every delivery to its ASN or PO
-
Scan and validate every inbound and returned item
-
Create manager-level signoff procedures for exceptions or damaged goods
3. Integrate and Validate Your Systems
Inventory accuracy breaks down when your POS, ERP, warehouse, and procurement tools don’t share real-time data. Every integration point is a potential breakage point.
-
Use middleware or APIs to keep systems in sync
-
Audit system logs and sync schedules monthly
-
Test updates and integrations in sandbox environments before live deployment
4. Monitor Shrinkage with Audit Logs
Shrinkage isn’t solved by locking doors—it’s solved by visibility and pattern recognition. Maintain logs for all adjustments, variances, and returns. Review those logs for consistent exceptions tied to staff, shifts, or product categories.
-
Implement role-based access and approval for stock adjustments
-
Run shrinkage reports by SKU or location
-
Investigate repeated discrepancies with cross-functional teams
5. Train for Accuracy — Not Just Speed
Process adherence is only as strong as your team’s understanding of why it matters. Ensure frontline teams understand the impact of bad inventory data—not just the mechanics of scanning or labeling.
-
Deliver inventory accuracy workshops quarterly
-
Align staff KPIs to accuracy metrics, not just speed
-
Create a feedback loop between ops, finance, and IT
Inventory accuracy isn’t about achieving perfection—it’s about creating a system that can detect and correct errors before they escalate. With the right tools, audits, and team culture, even large-scale operations can maintain inventory records that you can trust, plan around, and scale confidently It’s important to trace how inventory records become inaccurate in the first place—only then can you target the root causes.
Inaccurate inventory records don’t just throw off your stock counts — they disrupt customer trust, inflate operating costs, and sabotage long-term growth. The good news? These issues aren’t permanent. With the right systems, smarter checks, and strategic tools in place, you can regain control and turn your inventory into a competitive advantage.
Want to take the next step toward bulletproof inventory accuracy? Explore how leading retailers are fixing the root causes with real-time insights and smarter workflows.