Prevent Stockouts & Maximize Inventory Accuracy [2025 Guide]
Posted on March 13, 2025Effectively managing inventory to prevent stockouts is essential for maintaining customer satisfaction, profitability, and operational efficiency. Companies must proactively adopt strategies to prevent stockouts, ensuring sustained business growth and customer loyalty.
A stockout, also known as an “out-of-stock” situation, occurs when a business runs out of inventory for a particular product or SKU (stock keeping unit). In simple terms, it means you’re unable to fulfill customer orders immediately due to insufficient inventory on hand.
Stockouts can be highly damaging, leading to:
- Lost sales and revenue: Customers may purchase from competitors if products aren’t available.Prevent stockouts protects your revenue streams and enhances profitability.
- Dissatisfied customers due to delayed or canceled orders. Effective inventory strategies to prevent stockouts are critical for retaining valuable customers.
- Reduced customer loyalty and brand reputation damage, especially when stockouts occur repeatedly.
- Higher operational costs from rushed reordering or emergency shipping. Stockouts frequently necessitate emergency replenishments, significantly increasing operational expenses. Preventing stockouts minimizes unnecessary costs and maximizes operational efficiency.
Stop Losing Sales to Stockouts—Fix It Today!
Stockouts are costing you revenue. Take control and never miss another sale!
Inventory Accuracy
Inventory accuracy is a measure of how closely a business’s inventory records match the actual physical inventory available. High stock accuracy means the inventory recorded in your system precisely reflects what’s on your shelves or warehouse at any given time.
Inventory accuracy is calculated as:
Counted InventoryRecorded Inventory in System
× 100
Example: If your system shows 1,000 items and your physical count shows 970 items, your accuracy is 97%.
Importance of inventory accuracy
- Reliable forecasting: Accurate inventory ensures precise forecasting of demand and timely reordering.
- Reduces carrying costs: Prevents overstocking or understocking scenarios, minimizing inventory holding expenses.
- Enhances customer satisfaction: Avoids delays and canceled orders, leading to happier customers.
- Improves profitability: Accurate stock management directly impacts business efficiency, profitability, and competitive advantage.
One proven way to reduce errors and stockouts is evaluating the best cycle count tools for accuracy before your next upgrade.
Why Stockouts Matter: Understanding the True Financial Impact of Prevent Stockouts
📊 82% of Businesses Lose Customers Due to Stockouts—Don’t Be One of Them!
Stockouts can drive your customers away. Stay ahead and secure your sales!
Revenue Loss: Immediate Consequences of Stockouts
Stockouts lead directly to lost revenue because customers cannot purchase unavailable products. According to a global retail study, businesses typically lose around 4% of annual sales due to stockouts. For example, if your company generates $10 million in annual revenue, even a modest stockout rate of 5% can lead to $500,000 in lost sales annually.
Moreover, frequent stockouts drive customers to your competitors, amplifying these immediate revenue losses significantly. Many stockouts are simply the result of underlying inventory discrepancies — not actual supply chain issues. This article explains how those errors arise and how to prevent them.
Lost Customers and Decreased Loyalty
Research indicates that 30% of customers encountering a stockout switch to a competitor immediately. Worse still, long-term loyalty damage can result, with up to 40% never returning. For instance, a retail brand experiencing consistent stockouts might permanently lose repeat customers whose average lifetime value (LTV) could range from hundreds to thousands of dollars, depending on industry and product type. Imagine losing 30 loyal customers annually, each with an LTV of $10,000—that’s a potential long-term revenue loss of $300,000 each year.
Increased Operational Costs
When stockouts occur, businesses often rush to replenish inventory, incurring additional expenses such as expedited shipping fees, emergency procurement costs, overtime labor, and increased warehousing charges. These expenses can quickly escalate. For example, expediting replenishment shipments by air instead of sea freight may increase logistics costs by 30% or more, directly cutting into profit margins.
Damage to Brand Reputation
Repeated stockouts harm your company’s brand reputation, eroding customer trust and weakening your market position. Negative customer reviews can proliferate on platforms like Google and social media, deterring potential customers and leading to substantial future revenue losses. According to studies, a single negative online review can drive away approximately 22% of prospects. Considering an average customer value of $500, losing just 20 prospects from a single negative review translates into an immediate loss of $4,400 in potential revenue.
Prevent stockouts is crucial for sustainable profitability.
Managing Dead Stock: Strategies to Enhance Inventory Efficiency
We’ve Helped 500+ Companies Fix Their Inventory—You’re Next!
Don’t let inventory issues slow your business. Get expert solutions today!
What Is Dead Stock?
Dead stock refers to inventory items that have remained unsold for extended periods and are unlikely to sell in the future. These items occupy valuable warehouse space and tie up significant working capital without generating revenue, severely impacting business profitability and efficiency. Proper dead stock management is critical to prevent stockouts and ensure warehouse efficiency.
Financial Impact & Hidden Costs of Dead Stock
Holding excess dead stock significantly impacts financial performance. Strategies aimed at prevent stockouts help reduce dead stock accumulation and associated costs.
Dead stock doesn’t just represent sunk inventory costs; it also creates numerous hidden expenses, including:
- Storage costs (space, utilities, insurance)
- Depreciation and write-offs
- Opportunity costs (funds tied up that could otherwise be invested productively)
For instance, holding $50,000 worth of unsellable products could cost your business an additional 20-30% annually in warehousing, depreciation, and management fees—resulting in losses exceeding $10,000 each year.
Proven Strategies to Manage Dead Stock
Clearance Sales
Offering clearance discounts can rapidly clear excess inventory. Strategically discounting dead stock items helps quickly recover at least part of the inventory cost, freeing up warehouse space for more profitable products. For instance, a well-executed clearance sale can recoup 40–60% of the original investment, significantly mitigating losses.
Re-marketing or Repurposing Stock
Consider creative strategies such as bundling slow-moving products with fast-moving ones, or repurposing dead stock items for alternative markets. For example, re-marketing winter apparel during offseason promotions or bundling slow-selling items with popular products can enhance inventory turnover and reduce losses.
Optimal Ordering and Forecasting
Prevent future dead stock accumulation by enhancing your inventory forecasting and ordering processes. Utilize advanced forecasting software tools to anticipate demand accurately, ensuring purchases align closely with actual market requirements. Regular inventory analysis, combined with predictive analytics, helps businesses prevent overstocking and ensure optimal stock levels, significantly reducing the risk of dead stock.
By implementing these proactive strategies, businesses can reduce the occurrence of dead stock, freeing up critical resources to improve overall profitability and operational efficiency.
Root Causes of Inventory Stockouts
Prevent stockouts severely impact profitability, customer satisfaction, and operational efficiency. Understanding their root causes is crucial for implementing effective preventative strategies.
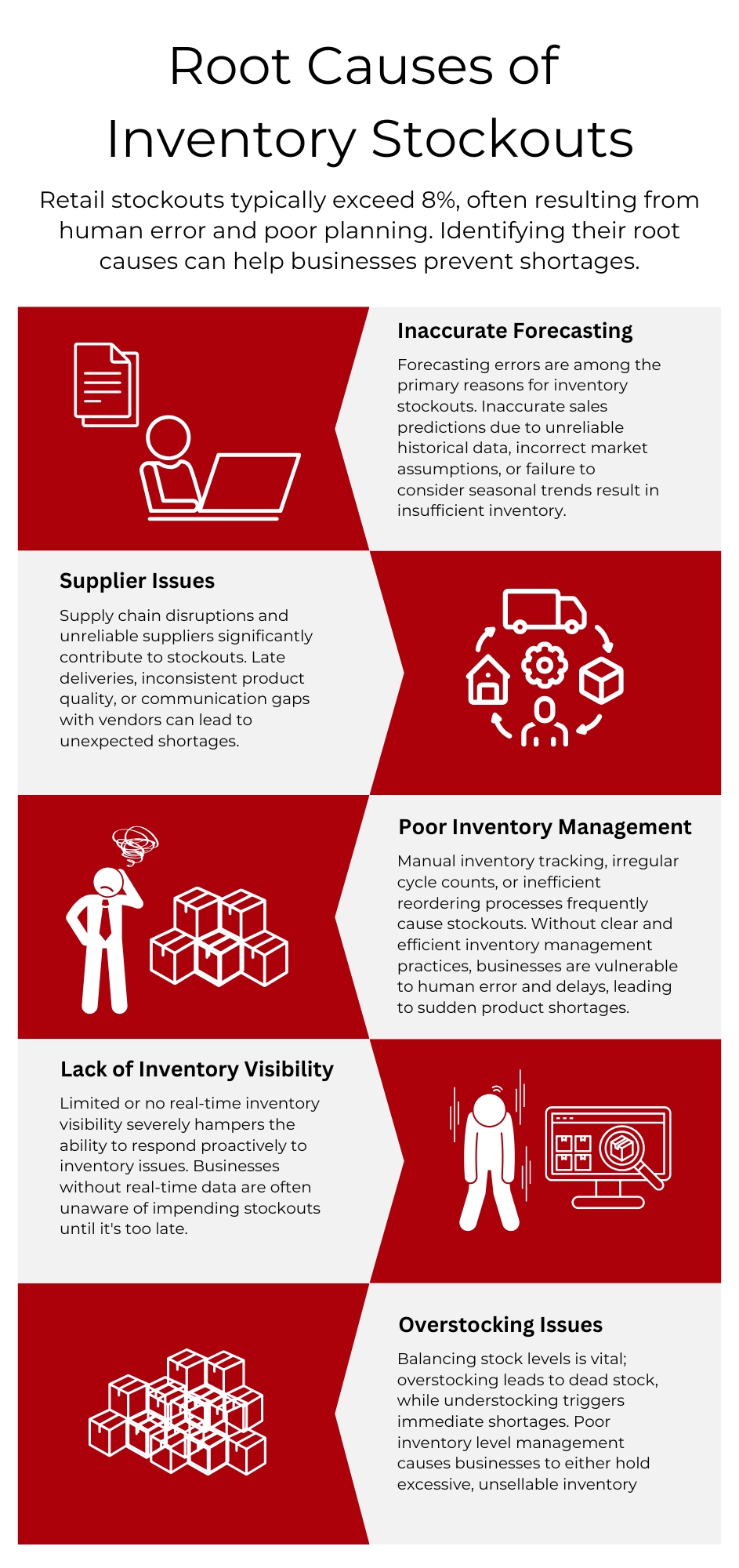
Inaccurate Forecasting & Poor Data
Forecasting errors are among the primary reasons for inventory stockouts. Inaccurate sales predictions due to unreliable historical data, incorrect market assumptions, or failure to consider seasonal trends result in insufficient inventory. For instance, if sales forecasts underestimate actual demand by 20%, businesses risk being short-stocked precisely when customer demand peaks.
Poor forecasting accuracy contributes significantly to stockouts. Accurate forecasting is essential for preventing stockouts.
Supplier Issues & Vendor Management Problems
Supply chain disruptions and unreliable suppliers significantly contribute to stockouts. Late deliveries, inconsistent product quality, or communication gaps with vendors can lead to unexpected shortages. Effective vendor management and building strong supplier relationships are essential for maintaining consistent stock levels.
Unreliable suppliers lead to frequent stockouts. Establishing strong supplier relationships helps prevent stockouts.
Poor Inventory Management Practices
Manual inventory tracking, irregular cycle counts, or inefficient reordering processes frequently cause stockouts. Without clear and efficient inventory management practices, businesses are vulnerable to human error and delays, leading to sudden product shortages. Streamlined, automated inventory management solutions can significantly mitigate these risks.
Inefficient inventory practices cause errors and shortages. Advanced inventory management prevents stockouts efficiently.
Lack of Inventory Visibility
Limited or no real-time inventory visibility severely hampers the ability to respond proactively to inventory issues. Businesses without real-time data are often unaware of impending stockouts until it’s too late. Advanced technology solutions such as real-time tracking software or RFID systems are crucial to maintaining visibility and avoiding inventory blind spots. RFID’s edge in reducing human error is clear when you compare it head-to-head with barcode scanning in this detailed tracking system comparison.
Without real-time inventory visibility, businesses risk sudden stockouts. Enhanced visibility effectively prevents stockouts.
Overstocking and Understocking Issues
Balancing stock levels is vital; overstocking leads to dead stock, while understocking triggers immediate shortages. Poor inventory level management causes businesses to either hold excessive, unsellable inventory or run into stockouts frequently. Leveraging advanced inventory analytics and precise reorder point calculations helps optimize stock levels, preventing both extremes effectively.
Addressing these root causes through proactive management and technological integration ensures your business minimizes stockouts, maximizing customer satisfaction, revenue potential, and operational efficiency.
Optimal stock level management helps prevent stockouts and controls inventory costs.
Best Practices to Manage and Prevent Stockouts
Effectively managing inventory requires a strategic approach that addresses root causes systematically. Here are proven best practices for preventing stockouts, enhancing stock control, and ensuring business profitability.
Prevent Stockouts with Demand Forecasting
Precise demand and forecasting is crucial for ensuring optimal inventory management. Implement advanced forecasting software to analyze historical data, seasonal trends, and market variables. For example, a retail business using precise forecasting tools can reduce forecast errors from 25% to under 10%, dramatically lowering stockout risk.
Cycle Counts & Inventory Audits
Perform regular cycle counts and inventory audits to maintain inventory accuracy. For instance, monthly cycle counts involving smaller inventory samples help detect discrepancies early, allowing prompt corrections before stock discrepancies lead to shortages.
Real-time Inventory Tracking to Prevent Stockouts
Leverage technology such as real-time tracking software, RFID, or barcode systems to enhance inventory visibility. Real-time tracking allows instant adjustments to inventory levels, preventing unexpected stockouts. Businesses implementing real-time tracking often see accuracy improvements above 95%.
Optimal Safety Stock Management
Establish optimal safety stock levels to act as a buffer against fluctuations in demand and supply. Calculate safety stock based on accurate forecasts, lead times, and service level goals. Properly managed safety stock can reduce stockouts by up to 60% without creating excess inventory.
Robust Cross-Department Collaboration
Encourage collaboration between sales, procurement, and warehouse teams to synchronize inventory management decisions. Effective communication between these departments ensures alignment, reduces ordering mistakes, and enhances responsiveness to potential shortages.
Building Strong Supplier Relationships
Maintain robust, communicative relationships with suppliers. Utilize vendor scorecards, performance reviews, and regular meetings to ensure reliability and responsiveness. Businesses with strong supplier relationships experience fewer disruptions and faster resolution of potential shortages.
Handling Stockout Situations Effectively
When stockouts occur, follow clear, actionable steps:
- Immediately Notify Customers: Proactively inform customers of delays and offer alternatives.
- Prioritize Replenishment: Expedite inventory replenishment through priority shipping methods and alternative suppliers if necessary.
- Offer Alternatives: Suggest similar or upgraded products to maintain customer satisfaction.
- Communicate Transparently: Provide clear timelines and consistent updates until product availability is restored.
Actionable Steps To Improving Inventory Accuracy
🕵️ We Bet You’re Losing Money on Inventory—Want to Prove Us Wrong?
Hidden losses could be eating into your profits. Let’s uncover them together!
Regular Inventory Audits & Cycle Counts
Regular inventory audits and cycle counts are fundamental practices to maintain accurate inventory records. Here’s a clear, step-by-step guide:
- Step 1: Schedule Frequent Cycle Counts
Schedule weekly or monthly counts rather than annual physical counts to detect discrepancies early. - Step 2: Identify Items for Counting
Use the ABC analysis method:- A-items: High-value or fast-moving products counted monthly.
- B-items: Count quarterly.
- C-items: Count semi-annually.
- Step 2: Prepare Inventory Count Sheets
Clearly document SKUs, current system quantities, and locations for easy reference. - Step 3: Conduct Physical Counts
Count items physically and accurately without prior knowledge of expected quantities to prevent bias. - Step 4: Compare and Investigate Variances
Document discrepancies and investigate causes, immediately correcting inaccuracies. - Step 5: Adjust and Document Findings
Record adjustments into inventory management software to reflect accurate stock levels.
Enhanced Warehouse Organization & Stock Storage
Proper warehouse organization significantly boosts inventory accuracy. Consider these practical tips:
- Clearly label bins, shelves, and product locations.
- Arrange frequently picked products near dispatch areas to reduce errors.
- Implement the FIFO (First-In-First-Out) inventory method to reduce obsolescence and ensure efficient stock rotation.
- Regularly inspect and reorganize storage areas for optimum efficiency.
Practical Employee Training & SOPs
Train warehouse employees thoroughly in inventory management best practices:
- Develop clear standard operating procedures (SOPs) for inventory handling.
- Regularly update training programs as processes evolve or new technologies are adopted.
- Encourage reporting discrepancies immediately to maintain continuous accuracy.
Reducing Safety Stock Without Increasing Risk
Minimizing safety stock intelligently improves cash flow without risking stockouts:
- Regularly review safety stock calculations based on demand variability, supplier lead times, and historical usage.
- Optimize reorder points with precise forecasting tools and inventory management software.
- Adjust safety stock dynamically based on seasonal demand fluctuations or supplier reliability.
The Critical Role of Technology in Modern Inventory Management
Advanced Inventory Management Systems & Software
Modern inventory management software plays a pivotal role in maintaining inventory accuracy and efficiency. Technology solutions like Datascan enhance stock accuracy. These advanced systems provide:
- Real-time Inventory Tracking: Ensure up-to-the-minute visibility on stock levels, helping businesses react quickly to potential shortages.
- Automated Reorder Processes: Set automated reorder points that trigger restocking processes instantly when stock levels fall below predefined thresholds, significantly minimizing the risk of stockouts.
Real-time Inventory Tracking Solutions
Real-time inventory tracking allows businesses to gain immediate visibility into inventory levels, dramatically enhancing accuracy and responsiveness. This technology significantly reduces human error, often achieving inventory accuracy rates above 98%. For instance, a business using RFID or barcode systems can immediately pinpoint product locations, quantities, and movements, eliminating guesswork and errors.
Automating Reorder Processes
Automated reordering streamlines inventory replenishment, drastically reducing the likelihood of running out of critical products. Automation ensures products are reordered at precisely calculated times, preventing delays caused by human oversight. For example, automation reduces manual ordering errors and associated costs by up to 30%, improving overall profitability.
Artificial Intelligence & Predictive Analytics
Artificial Intelligence (AI) and predictive analytics dramatically enhance forecasting accuracy, helping businesses optimize stock levels by:
- Analyzing historical sales data, seasonal trends, and market patterns.
- Predicting customer demand with significantly higher accuracy compared to traditional forecasting methods.
Companies leveraging AI-driven predictive analytics have experienced inventory accuracy improvements of up to 30%, significantly reducing stockouts and overstock scenarios.
IoT (Internet of Things) in Inventory Management
The Internet of Things (IoT) revolutionizes inventory management through connected sensors and devices. IoT technology provides:
- Real-time Data Collection: Sensors inventory tracking continuously, updating inventory status automatically.
- RFID and Barcode Tracking: Instantly track goods entering and exiting warehouses.
For example, RFID-enabled warehouses typically achieve inventory accuracy rates exceeding 98%, significantly higher than manual or traditional tracking methods.
How AI Reduces Stockouts and Optimizes Stock Levels
Artificial Intelligence enhances inventory management by:
- Improving Demand Forecast Accuracy: AI algorithms predict customer needs more precisely.
- Optimizing Safety Stock Levels: Automatically adjusts safety stock levels based on real-time data, minimizing unnecessary inventory without increasing stockout risk.
Businesses employing AI tools typically see reduced inventory carrying costs and increased product availability, directly impacting profitability and operational efficiency.
Leveraging these advanced technological solutions significantly strengthens your ability to manage inventory effectively, optimize costs, reduce stockouts, and enhance overall profitability.
How Technology Helps Reduce Stockouts
Advanced technology solutions have consistently proven effective in reducing stockouts, increasing efficiency, and boosting profitability. Here are real-world cases and clear demonstrations of these benefits:
Real-world Case Study 1: Retail Chain Implements Real-time Inventory Tracking |
---|
A major retail chain struggled with frequent stockouts due to inaccuracies in inventory records and manual replenishment processes. They implemented an advanced real-time inventory tracking solution using barcode scanning and automated reordering. Within six months:
|
Real-world Case Study 2: AI-Powered Predictive Analytics for a Consumer Electronics Brand |
---|
A leading consumer electronics brand experienced chronic issues of overstocking slow-moving items while frequently stockouting bestsellers. After adopting AI-driven predictive analytics software:
|
Clearly Demonstrated Benefits of Technology:
- Improved Profitability: Enhanced inventory management reduces holding costs and increases sales by ensuring product availability.
- Greater Efficiency: Automating processes minimizes manual work, accelerating operations and freeing staff to focus on customer engagement.
- Reduced Human Errors: Leveraging technology such as barcoding, RFID, and automated ordering significantly cuts down on data-entry and tracking errors, improving overall operational accuracy.
Choosing the Right Inventory Management Technology
Selecting the right inventory management technology is crucial for optimizing inventory processes and preventing stockouts. Here’s a practical guide to ensure your business selects a solution perfectly aligned with your operational needs and strategic goals:
Clear Criteria for Evaluating Inventory Management Systems
When choosing an inventory management tool, evaluate the following essential features to prevent stockouts:
- Real-time Inventory Tracking:
- Ensure the system provides live inventory visibility across all warehouses and stores.
- Forecasting and Demand Planning:
- Confirm the software offers robust forecasting capabilities to predict future demand accurately.
- Automated Reordering Capabilities:
- Look for systems that automate reorder points and replenishment, eliminating manual monitoring and human errors.
- Integration Capabilities:
- Ensure compatibility and seamless integration with existing ERP, POS, and accounting systems for real-time data synchronization.
- Reporting & Analytics:
- Opt for software providing comprehensive analytics, enabling clear insights into inventory performance metrics and trends.
- User-Friendly Interface:
- Ensure ease-of-use and intuitive navigation to encourage adoption and minimize training time.
- Mobile Accessibility:
- Verify the technology supports mobile devices to allow real-time inventory management from any location.
- Integration Capabilities:
- Confirm the solution integrates smoothly with your existing accounting, eCommerce, and ERP systems.
Checklist for Selecting Inventory Management Software |
---|
|
By carefully evaluating technology against these essential criteria, you ensure your investment effectively reduces stockouts, streamlines operations, and maximizes profitability.
Reducing Safety Stock Without Risking Stockouts
Safety stock refers to extra inventory held to mitigate risks of stockouts due to demand fluctuations or supplier delays. Maintaining safety stock is crucial as it acts as a buffer, ensuring uninterrupted service and maintaining customer satisfaction. Properly calculated safety stock effectively prevents stockouts.
Why Safety Stock Matters
- Prevents Stockouts: Safety stock provides insurance against unforeseen demand spikes or supply disruptions.
- Improves Customer Satisfaction: Ensures products remain available, enhancing reliability and customer trust.
- Balances Supply and Demand: Absorbs variability in demand forecasting and supplier performance, creating stability in operations.
The Financial Risks of Excess Safety Stock
While safety stock is beneficial, excess safety stock ties up valuable capital, increasing inventory costs, storage expenses, and risks of obsolescence. For example, holding just 10% more safety stock than needed could cost a medium-sized business tens of thousands of dollars annually, significantly impacting profitability.
Proven Methods to Safely Reduce Safety Stock Without Increasing Stockouts
Follow these clear, proven steps to strategically reduce safety stock without jeopardizing stock availability:
Step 1: Improve Demand Forecast Accuracy
Enhance your forecasting precision by leveraging advanced analytics or AI-driven solutions, reducing demand variability and the need for excessive safety stock.
Step 2: Optimize Supplier Relationships
Strengthen supplier reliability through better communication, regular performance reviews, and clear expectations. Reliable suppliers decrease lead times and variability, enabling lower safety stock.
Step 3: Shorten Lead Times
Work with suppliers to minimize lead times, allowing your business to react swiftly to changes in demand without needing large safety buffers.
Step 4: Regular Review and Adjustment
Periodically reassess safety stock levels based on updated forecasting data, market conditions, and seasonal demand fluctuations to ensure they remain optimized.
Step 4: Leverage Advanced Inventory Software
Use inventory management software and predictive analytics to calculate optimal safety stock levels dynamically, based on real-time data rather than historical guesswork.
Summary: Strategic Takeaways
Effective management of stockouts and inventory accuracy has direct and significant financial benefits. Here’s a concise summary of actionable strategies and insights:
Key Takeaways:
-
Inventory accuracy is key to prevent stockouts: Regular cycle counts, audits, and real-time tracking are foundational practices for maintaining inventory accuracy above 95%.
- Financial Costs of Stockouts: Stockouts directly cause revenue loss, customer dissatisfaction, increased operational expenses, and damage brand reputation.
- Dead Stock Management: Regular clearance sales, strategic re-marketing, and optimal forecasting help prevent dead stock accumulation, saving operational costs and improving cash flow.
-
Technology adoption and accurate forecasting effectively prevent stockouts: Implementing advanced inventory management software, automation, AI-driven predictive analytics, and IoT solutions significantly enhances inventory accuracy, reduces human errors, and prevents costly stockouts.
- Optimal Safety Stock Levels: Accurately calculate safety stock through predictive analytics and supplier reliability to balance availability and inventory costs effectively.
Immediate Next Steps:
- Audit your current inventory practices to identify weaknesses.
- Adopt robust inventory management systems with real-time tracking and automation.
- Strengthen supplier relationships and optimize reorder processes.
- Regularly review inventory performance and continuously adapt strategies.
By consistently applying these strategic practices, businesses can substantially improve profitability, enhance operational efficiency, and achieve sustainable inventory management success.
Real-Life Success Stories Of Prevent Stockouts
Real-world examples clearly demonstrate the power of strategic inventory management in reducing stockouts and boosting profitability.
Case Study 1: Successful Reduction of Stockouts |
---|
A global apparel retailer faced frequent stockouts due to unreliable manual inventory tracking and inadequate forecasting. After implementing real-time inventory management software integrated with predictive analytics, they experienced:
|
Case Study 2: Enhancing Inventory Accuracy & Profitability |
---|
A large automotive parts distributor struggled with persistent inaccuracies in inventory records, leading to excess holding costs and frequent shortages. After adopting RFID technology for real-time tracking and regular cycle counting methods:
|
These real-life examples demonstrate that addressing stockouts and improving inventory accuracy through strategic technology adoption significantly enhances business performance, profitability, and long-term customer relationships.
Ready to Prevent Stockouts and Boost Inventory Accuracy?
Don’t let inventory inaccuracies or stockouts limit your business potential. Take control today by adopting advanced inventory management solutions tailored to your specific business needs.
Every Click Delayed = A Potential Lost Sale. Act Now!
📞 Schedule a Free Consultation Today & Take Control of Your Inventory!